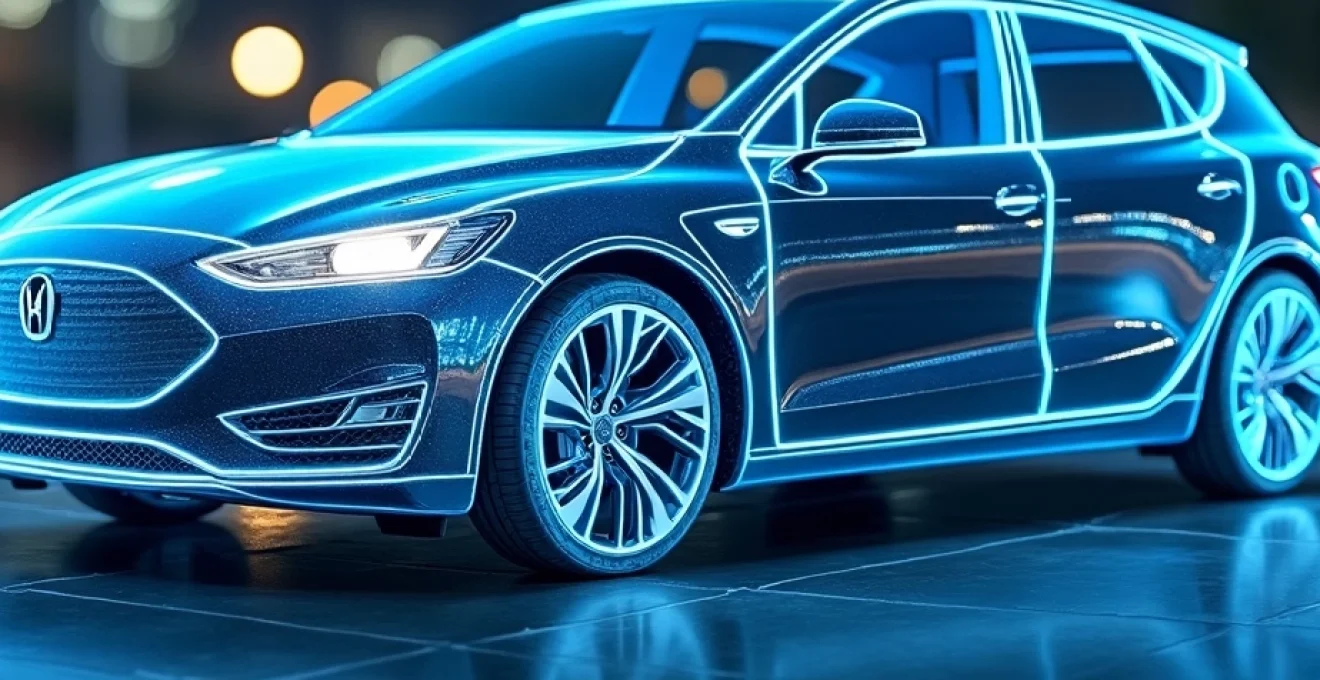
The automotive landscape is undergoing a seismic shift as electric hybrid vehicles gain momentum, reshaping the industry's future. This revolutionary technology combines the best of both worlds: the efficiency of electric motors and the reliability of traditional combustion engines. As environmental concerns grow and fuel prices fluctuate, consumers and manufacturers alike are turning to hybrid vehicles as a viable solution for sustainable transportation.
Hybrid powertrains represent a critical stepping stone in the evolution of automotive technology, bridging the gap between conventional gasoline-powered cars and fully electric vehicles. By harnessing the power of both electric motors and internal combustion engines, hybrids offer improved fuel economy, reduced emissions, and enhanced performance. This innovative approach to vehicle design is not only transforming the driving experience but also challenging automakers to adapt their production processes and supply chains.
Evolution of hybrid powertrains: from toyota prius to modern PHEVs
The journey of hybrid powertrains began in earnest with the introduction of the Toyota Prius in 1997. This groundbreaking vehicle marked the start of a new era in automotive engineering, combining a gasoline engine with an electric motor to achieve unprecedented fuel efficiency. The success of the Prius paved the way for widespread adoption of hybrid technology across various vehicle segments.
As the technology matured, automakers began experimenting with different hybrid configurations. Mild hybrids, which use a small electric motor to assist the combustion engine, gained popularity due to their cost-effectiveness and ease of implementation. Full hybrids, capable of running on electric power alone for short distances, became the gold standard for fuel efficiency in urban environments.
The latest evolution in hybrid technology comes in the form of Plug-in Hybrid Electric Vehicles (PHEVs). These advanced hybrids feature larger battery packs that can be charged from external power sources, allowing for extended electric-only driving ranges. PHEVs offer the flexibility of pure electric driving for short trips while retaining the long-range capability of traditional hybrids, making them an attractive option for consumers looking to reduce their carbon footprint without sacrificing convenience.
Battery technology advancements: lithium-Ion to solid-state
At the heart of every hybrid vehicle lies its battery pack, and the advancements in battery technology have been nothing short of revolutionary. Early hybrids relied on nickel-metal hydride (NiMH) batteries, which were reliable but heavy and limited in capacity. The introduction of lithium-ion batteries marked a significant leap forward, offering higher energy density, faster charging times, and improved longevity.
Today, researchers and manufacturers are pushing the boundaries of battery technology even further, with solid-state batteries emerging as the next frontier. These innovative power sources promise even higher energy densities, faster charging capabilities, and enhanced safety compared to their liquid electrolyte counterparts. The potential of solid-state batteries to revolutionize hybrid and electric vehicle performance is immense, potentially doubling driving ranges and significantly reducing charging times.
High-density Nickel-Manganese-Cobalt (NMC) cathodes
One of the key advancements in lithium-ion battery technology has been the development of high-density Nickel-Manganese-Cobalt (NMC) cathodes. These advanced materials allow for greater energy storage capacity within the same physical battery size, translating to extended driving ranges for hybrid vehicles. The latest NMC cathodes boast nickel content of up to 80%, significantly boosting energy density while reducing the reliance on costly and ethically problematic cobalt.
Silicon-based anodes for increased energy density
On the anode side of the battery, silicon is emerging as a game-changing material. Silicon anodes can theoretically store up to ten times more lithium ions than traditional graphite anodes, potentially leading to dramatic increases in battery capacity. However, challenges related to silicon's tendency to expand and contract during charging cycles are still being addressed through innovative nanostructuring techniques and composite materials.
Solid Electrolyte Interphase (SEI) formation in hybrid batteries
The Solid Electrolyte Interphase (SEI) is a critical component in lithium-ion batteries, forming a protective layer between the electrode and electrolyte. In hybrid vehicle applications, where batteries undergo frequent charge and discharge cycles, optimizing SEI formation is crucial for long-term battery performance and longevity. Researchers are developing advanced electrolyte additives and surface coatings to enhance SEI stability, potentially extending battery life and improving overall vehicle reliability.
Quantum glass battery potential in future hybrids
Looking further into the future, quantum glass batteries represent a potentially revolutionary technology for hybrid vehicles. These batteries, which utilize a glass electrolyte and lithium or sodium metal electrodes, promise exceptional energy density, ultra-fast charging capabilities, and enhanced safety. While still in the early stages of development, quantum glass batteries could potentially overcome many of the limitations of current lithium-ion technology, ushering in a new era of high-performance, long-range hybrid vehicles.
Regenerative braking systems: efficiency and energy recovery
Regenerative braking systems are a cornerstone of hybrid vehicle efficiency, transforming the kinetic energy of a moving vehicle into electrical energy that can be stored in the battery for later use. This innovative technology not only improves overall fuel economy but also reduces wear on traditional friction brakes, potentially lowering maintenance costs for hybrid vehicle owners.
The effectiveness of regenerative braking systems has improved significantly since their introduction. Modern hybrids can recover up to 70% of the vehicle's kinetic energy during deceleration, a substantial improvement over early systems. This recaptured energy is then used to power the electric motor during acceleration or to maintain vehicle systems, reducing the load on the combustion engine and further improving fuel efficiency.
Advanced regenerative braking systems in today's hybrids often feature multiple levels of energy recovery, allowing drivers to adjust the intensity of regeneration to suit their driving style or road conditions. Some systems even use predictive technology and GPS data to optimize energy recovery based on upcoming terrain or traffic patterns, maximizing efficiency in real-world driving scenarios.
Plug-in hybrid electric vehicles (PHEVs): extended range and charging infrastructure
Plug-in Hybrid Electric Vehicles (PHEVs) represent the cutting edge of hybrid technology, offering the best of both worlds: the ability to drive on pure electric power for daily commutes and the flexibility of a gasoline engine for longer trips. PHEVs typically feature larger battery packs than traditional hybrids, allowing for electric-only ranges of 30 to 50 miles or more, depending on the model.
The success of PHEVs is closely tied to the development of charging infrastructure. As more public charging stations become available, the practicality of PHEVs increases, allowing owners to maximize their electric driving and minimize gasoline consumption. Many governments and private companies are investing heavily in expanding charging networks, recognizing the critical role they play in the adoption of electrified vehicles.
J1772 vs. CHAdeMO charging standards for PHEVs
Two primary charging standards have emerged for PHEVs: J1772 and CHAdeMO. The J1772 standard, also known as SAE J1772, is the most common in North America and is compatible with most PHEVs and electric vehicles. It supports Level 1 (120V) and Level 2 (240V) charging, with charging times ranging from a few hours to overnight, depending on the battery capacity and charging speed.
CHAdeMO, on the other hand, is a DC fast-charging standard primarily used by Japanese automakers. While less common for PHEVs, CHAdeMO chargers can provide rapid charging capabilities, potentially adding significant range in just 30 minutes. The CHAdeMO
protocol continues to evolve, with the latest version supporting charging rates of up to 400kW, promising even faster charging times for future PHEVs equipped with this technology.
Vehicle-to-grid (V2G) technology integration
Vehicle-to-Grid (V2G) technology is an exciting development in the world of PHEVs, allowing these vehicles to not only draw power from the grid but also feed it back when needed. This bidirectional flow of energy has the potential to revolutionize power management, using PHEV batteries as a distributed energy storage system to balance grid loads during peak demand periods.
V2G technology could provide PHEV owners with additional value, potentially earning revenue by selling excess energy back to the grid or using their vehicle's battery to power their home during outages. As smart grid technologies advance, the integration of V2G-enabled PHEVs into the broader energy ecosystem is likely to become increasingly seamless and beneficial for both vehicle owners and utility companies.
BMW i3 REx: Range Extender implementation case study
The BMW i3 with Range Extender (REx) offers an interesting case study in PHEV design. Unlike traditional PHEVs, which use a full-size gasoline engine, the i3 REx employs a small, 647cc two-cylinder motorcycle engine as a generator to extend the vehicle's range. This innovative approach allows the i3 to maintain its primarily electric-driven character while providing the peace of mind of extended range when needed.
The i3 REx's unique design highlights the flexibility of PHEV powertrains, demonstrating how automakers can tailor hybrid systems to meet specific vehicle requirements and market demands. This approach has inspired other manufacturers to explore similar range-extender concepts, potentially leading to a new subcategory of PHEVs optimized for predominantly electric operation with minimal reliance on internal combustion.
Mitsubishi Outlander PHEV: All-Wheel drive hybrid system
The Mitsubishi Outlander PHEV showcases another innovative approach to hybrid powertrain design, particularly in the SUV segment. It features a dual-motor all-wheel-drive system, with electric motors powering both the front and rear axles. This configuration not only provides excellent traction and performance but also allows for precise torque vectoring, enhancing handling and stability.
The Outlander PHEV's powertrain demonstrates how hybrid technology can be adapted to meet the demands of larger vehicles traditionally associated with higher fuel consumption. By leveraging the instant torque of electric motors and the efficiency of a purpose-designed gasoline engine, the Outlander PHEV achieves a balance of performance, efficiency, and versatility that has made it one of the best-selling PHEVs globally.
Mild hybrid systems: 48V architecture and belt-driven starter generators
Mild hybrid systems represent a cost-effective approach to hybridization, offering many of the benefits of full hybrid systems at a fraction of the cost. These systems typically utilize a 48V electrical architecture, which provides more power than traditional 12V systems while avoiding the complexity and cost of high-voltage systems used in full hybrids.
At the heart of many mild hybrid systems is the Belt-Driven Starter Generator (BSG), also known as a Belt-Integrated Starter Generator (BISG). This compact device replaces the traditional alternator and starter motor, providing several key functions:
- Quick and smooth engine start/stop operation
- Regenerative braking to capture energy during deceleration
- Electric boost to assist the engine during acceleration
- Efficient power generation for vehicle electrical systems
The 48V architecture allows for the integration of more powerful electric accessories, such as electric superchargers or active suspension systems, further enhancing vehicle performance and efficiency. As automakers strive to meet increasingly stringent emissions regulations, mild hybrid systems are being adopted across a wide range of vehicle segments, from compact cars to luxury SUVs.
Impact on automotive supply chain and manufacturing processes
The rise of hybrid vehicles is having a profound impact on the automotive supply chain and manufacturing processes. Traditional suppliers are being challenged to adapt their product offerings to meet the needs of electrified powertrains, while new players specializing in electric motors, power electronics, and battery systems are entering the market.
This shift is reshaping the entire automotive ecosystem, from raw material sourcing to final assembly. Manufacturers are investing heavily in retooling their production lines to accommodate hybrid powertrains, often creating flexible manufacturing systems capable of producing both conventional and electrified vehicles on the same line.
Shift from internal combustion engine to electric powertrain production
The transition from internal combustion engines to electric powertrains represents a significant challenge for established automotive suppliers. Companies that have traditionally focused on components such as fuel injection systems, exhaust systems, and multi-speed transmissions are now pivoting towards electric motor production, power electronics, and single-speed gearboxes.
This shift requires substantial investment in new technologies and manufacturing processes. For example, the production of electric motors involves precision winding of copper wire and assembly of complex rotor and stator components, requiring different skill sets and equipment compared to traditional engine manufacturing.
Battery cell manufacturing: gigafactories and vertical integration
Battery production has become a critical component of the hybrid and electric vehicle supply chain. The concept of "gigafactories" - massive, highly automated battery production facilities - has gained traction as automakers seek to secure their battery supply and reduce costs through economies of scale. These facilities represent a significant departure from traditional automotive manufacturing, incorporating chemical processing and advanced material science alongside more familiar assembly processes.
Many automakers are pursuing vertical integration strategies, investing in their own battery production capabilities or forming joint ventures with established battery manufacturers. This approach allows for greater control over the supply chain and the potential for technological differentiation in a critical component of hybrid and electric vehicles.
Rare earth elements sourcing for electric motors
The production of electric motors for hybrid vehicles relies heavily on rare earth elements, particularly neodymium and dysprosium, which are used in the powerful permanent magnets that drive these motors. The sourcing of these materials has become a strategic concern for many automakers, as the global supply is currently dominated by a small number of countries, primarily China.
Efforts are underway to diversify the supply of rare earth elements, with new mining projects being developed in various parts of the world. Additionally, research into alternative motor designs that reduce or eliminate the need for rare earth magnets is ongoing, potentially leading to more sustainable and geopolitically stable supply chains for hybrid vehicle components.
Just-in-time manufacturing adaptation for hybrid components
The complexity of hybrid powertrains, with their combination of mechanical and electrical systems, presents challenges for traditional just-in-time (JIT) manufacturing processes. The integration of battery packs, power electronics, and electric motors requires new approaches to inventory management and production scheduling.
Manufacturers are adapting their JIT systems to accommodate the unique requirements of hybrid vehicle production. This may involve closer coordination with suppliers of critical electric components, implementation of advanced tracking systems for high-value parts like battery cells, and the development of more flexible assembly processes that can handle the variability inherent in hybrid powertrain configurations.
As the automotive industry continues its transition towards electrification, the impact on manufacturing processes and supply chains will only grow more pronounced. Successful adaptation to these changes will be crucial for both established players and new entrants in the hybrid vehicle market, shaping the future of automotive production for decades to come.